From November 2023: RAISE3D First Metal Printing Service
If you are interested in having your prototypes made in metal using 3D printing, take a detailed look at the RAISE3D Forge1.
RAISE3D’s Forge1 can be used to print objects with the maximum size of 100x100x100 mm.
The complete RAISE3D “MetalFuse” system consists of 3 devices, the Forge1 for 3D printing, the debinding unit and the sintering furnace.
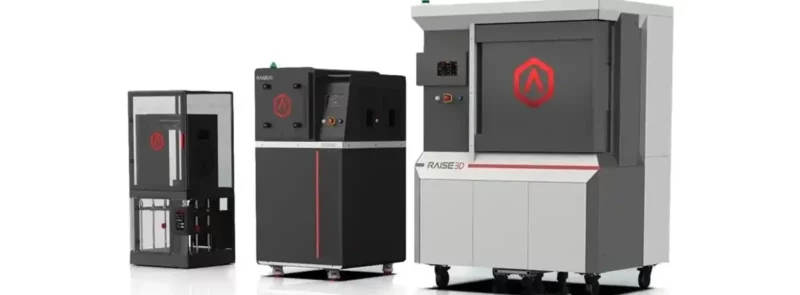
How does this process work?
The process consists of the following steps: Printing by filament, debinding and sintering.
- Printing by filament
The process begins with the creation of a digital 3D model of the desired metal part. This model is then layered in software and converted into a printable gcode.
In FDM metal 3D printing with the Forge1, we use a special metal filament consisting of a 316L or 17-4PH POM blend. The filament is fed into a pressure chamber, heated and melted. An extruder moves according to the instructions of the data in the gCode and deposits the molten metal filament layer by layer to build up the metal part.
The finished printed model is called a “green part.” - Debinding
After the “green compact” is printed, it still contains binder (POM), which is used to hold the “metal dust” together. In this step, the binder is removed from the printed part in the D200-E debinding unit using a cathalytic process. This process is called debinding. The result is a porous metal part, which of course does not have the final mechanical properties, is very brittle and is called “browning”. - Sintering
After debinding, the porous “browning” is placed in an S200-C sintering furnace. During sintering, the metal part is heated to a high temperature but not completely melted. The metal particles begin to diffuse and bond together, turning the porous part into a dense and strong metal part. This process improves the mechanical properties of the part, such as strength and durability.
After sintering, the finished metal model can undergo further post-processing steps, such as removing support structures and grinding or polishing to achieve the desired surface quality. The finished metal 3D print can then be used for a variety of applications, such as aerospace, automotive and medical.
During the sintering process, the size of the printed object is reduced by approx. 20 – 24% – this size change must therefore be taken into account before printing.
And this is where our 3D metal printing service comes into play:
RAISE3D First Metal Print Service
You create the 3D print file as your desired print object should look in the end.
On our website you buy a RAISE3D voucher for CHF 195.- and send us your STL file so that your print file can be checked and optimized by RAISE3D.
Afterwards, after successful verification of the 3D model, we will receive the print file as gCode, with which we will execute the print for you on our RAISE3D Forge1. Included in the CHF 195.- is a debinding and sintering voucher worth CHF 65.- to have the printed object debound and sintered afterwards.
The finished metal object will be back to you within approx. 2-3 weeks.
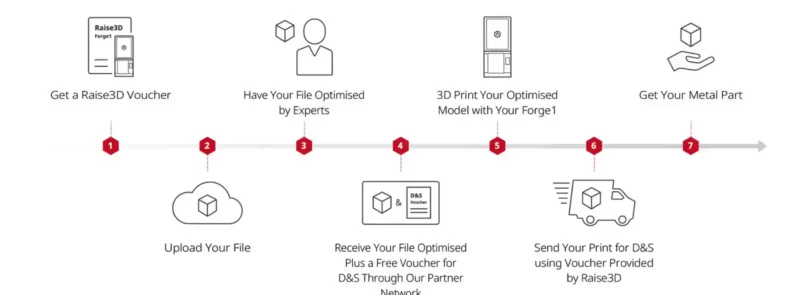
What is included in the RAISE3D First Metal Print Service?
For the single price of CHF 195.- you get:
- Validation and optimization of single parts according to the design guidelines
- RAISE3D recommendations for improvements and best settings for a perfect print
- Debinding and sintering voucher (D&S) through a network of reliable partners
- Guaranteed result or money back
Best print result or money back guarantee
We stand behind the quality of our work, that’s why we offer optimized 3D designs with the best print quality or a money back guarantee.
If you are not satisfied with the result, we will repeat the process (up to 2 times) to meet your expectations or we will give you a full refund.
With our money-back guarantee, you can be sure you’re getting the best value for your investment.
Would you like to know more?
Then get in touch with us or drop by our showroom in Weinfelden – we’ll be happy to advise you.